Products
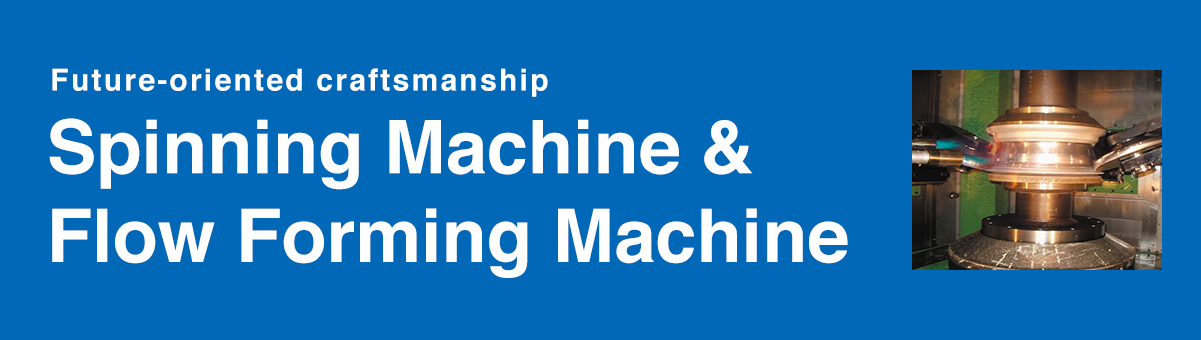

Features of flow forming (metal spinning)
The flow forming is a transforming process that a metal plate or cup-shaped metal workpiece is rotated over a mandrel while a roller deforms the workpiece, forcing it against the mandrel. The process allows you to stretch the material thinly, thicken it, or cleave and expand it as if working with dough. As a result, you can form metal into shapes that are not conceivable with traditional processing work. This process can be used to fabricate workpieces of a variety of shapes without leaving cutting flakes, offering greater freedom of component design. It can be roughly divided into the following process methods.

Features of Nihon Spindle Flow Forming (Spinning) machines
- Best cost performance with optimal design
- Machine specifications can be determined based on thrust measurement data obtained during the actual trials with R&D machine. Along with structural analysis, it is possible to offer “JUST-FIT” machine.
- Aggressive use of a servo motor driving method for lower running cost
- All roller units are driven by electric servo motors, which can reduce running cost by 30% to 50% against a conventional hydraulic servo method (compared to our company products). Reduction of hydraulic driving units leads to lower noise and less oil leakage.
- Independent roller control for various processes
- Each flow forming roller has their own control axis, which can be used to reduce cycle time by overlapping rollers. It is also easy to set each roller position for each axes by NC program.
- Adopt “Processing chamber” concept
- Processing chamber is completely isolated from the control unit and driving unit to avoid malfunction and other mechanical issues due to intrusion of coolant or sludge. This concept also offers easy cleaning of the machine.
- Optional mandrel exchange unit for smoother change-over
- Mandrel exchange unit and roller exchange unit are optionally available for smoother change-over due to a blocked top section of the machine.
- Flow Forming
- Force the material against a die so that it imprints the shape of the die.
- Flow Forming benefit [1]
- Pressing the material between a die and a roller can increase the density of the material’s tissues, substantially enhancing its strength. This process can reduce the thickness or eliminate the subsequent heat-treatment process.
- Flow Forming benefit [2]
- Tube necking, or partial reduction of tube thickuess makes it possible to thicken specified part where higher strength is required, which has been unachievable with any traditional method.
- Available machine types

Features of Nihon Spindle Flow Forming (Spinning) machines
- Best cost performance with optimal design
- Machine specifications can be determined based on thrust measurement data obtained during the actual trials with R&D machine. Along with structural analysis, it is possible to offer “JUST-FIT” machine.
- Aggressive use of a servo motor driving method for lower running cost
- All roller units are driven by electric servo motors, which can reduce running cost by 30% to 50% against a conventional hydraulic servo method (compared to our company products). Reduction of hydraulic driving units leads to lower noise and less oil leakage.
- Independent roller control for various processes
- Each flow forming roller has their own control axis, which can be used to reduce cycle time by overlapping rollers. It is also easy to set each roller position for each axes by NC program.
- Adopt “Processing chamber” concept
-
- Processing chamber is completely isolated from the control unit and driving unit to avoid malfunction and other mechanical issues due to intrusion of coolant or sludge. This concept also offers easy cleaning of the machine.
- Optional mandrel exchange unit for smoother change-over
-
- Mandrel exchange unit and roller exchange unit are optionally available for smoother change-over due to a blocked top section of the machine.
- Spinning
- Necking a tube, or partially reducing the thickness. A tube can be formed even with parts installed inside.
- Spinning benefits
- Even difficult-to-process materials as well as complex shapes that would require multiple dies in pressing process can usually be handled using only a single die. Curling and trimming can also be processed by changing tools during spinning.
- Available machine types

Features of Nihon Spindle Flow Forming (Spinning) machines
- Best cost performance with optimal design
- Machine specifications can be determined based on thrust measurement data obtained during the actual trials with R&D machine. Along with structural analysis, it is possible to offer “JUST-FIT” machine.
- Aggressive use of a servo motor driving method for lower running cost
- All roller units are driven by electric servo motors, which can reduce running cost by 30% to 50% against a conventional hydraulic servo method (compared to our company products). Reduction of hydraulic driving units leads to lower noise and less oil leakage.
- Independent roller control for various processes
- Each flow forming roller has their own control axis, which can be used to reduce cycle time by overlapping rollers. It is also easy to set each roller position for each axes by NC program.
- Adopt “Processing chamber” concept
-
- Processing chamber is completely isolated from the control unit and driving unit to avoid malfunction and other mechanical issues due to intrusion of coolant or sludge. This concept also offers easy cleaning of the machine.
- Optional mandrel exchange unit for smoother change-over
-
- Mandrel exchange unit and roller exchange unit are optionally available for smoother change-over due to a blocked top section of the machine.
- Cleaving
- Split the material into a Y- or T-shaped section. This method allows part integration, eliminating the need for welding.
- Example of benefits of Flow Forming and Cleaving
- Spline forming, which is usually made through machining, and hub forming, which is usually achieved by welding separate parts, can be simply done by welding-free, machining-free flow forming.
- Available machine types

Features of Nihon Spindle Flow Forming (Spinning) machines
- Best cost performance with optimal design
- Machine specifications can be determined based on thrust measurement data obtained during the actual trials with R&D machine. Along with structural analysis, it is possible to offer “JUST-FIT” machine.
- Aggressive use of a servo motor driving method for lower running cost
- All roller units are driven by electric servo motors, which can reduce running cost by 30% to 50% against a conventional hydraulic servo method (compared to our company products). Reduction of hydraulic driving units leads to lower noise and less oil leakage.
- Independent roller control for various processes
- Each flow forming roller has their own control axis, which can be used to reduce cycle time by overlapping rollers. It is also easy to set each roller position for each axes by NC program.
- Adopt “Processing chamber” concept
-
- Processing chamber is completely isolated from the control unit and driving unit to avoid malfunction and other mechanical issues due to intrusion of coolant or sludge. This concept also offers easy cleaning of the machine.
- Optional mandrel exchange unit for smoother change-over
-
- Mandrel exchange unit and roller exchange unit are optionally available for smoother change-over due to a blocked top section of the machine.
- Thickening
- Thicken the material to produce a partially thickened piece.
- Example of benefits from thickening and gear rolling process
- It is possible to integrate a disk plate, such as “Drive plate” and ring gear part in one solid part without welding process. Also it is possible to process O-ring groove and roll gear by imprinting the roller shape on the part.
- Available machine types

Features of Nihon Spindle Flow Forming (Spinning) machines
- Best cost performance with optimal design
- Machine specifications can be determined based on thrust measurement data obtained during the actual trials with R&D machine. Along with structural analysis, it is possible to offer “JUST-FIT” machine.
- Aggressive use of a servo motor driving method for lower running cost
- All roller units are driven by electric servo motors, which can reduce running cost by 30% to 50% against a conventional hydraulic servo method (compared to our company products). Reduction of hydraulic driving units leads to lower noise and less oil leakage.
- Independent roller control for various processes
- Each flow forming roller has their own control axis, which can be used to reduce cycle time by overlapping rollers. It is also easy to set each roller position for each axes by NC program.
- Adopt “Processing chamber” concept
-
- Processing chamber is completely isolated from the control unit and driving unit to avoid malfunction and other mechanical issues due to intrusion of coolant or sludge. This concept also offers easy cleaning of the machine.
- Optional mandrel exchange unit for smoother change-over
-
- Mandrel exchange unit and roller exchange unit are optionally available for smoother change-over due to a blocked top section of the machine.
- Gear-Rolling
- Transfer the contour of a roller to the material, making O-ring grooves or splines.
- Example of benefits from thickening and gear rolling process
- It is possible to integrate a disk plate, such as “Drive plate” and ring gear part in one solid part without welding process. Also it is possible to process O-ring groove and roll gear by imprinting the roller shape on the part.
- Available machine types

Features of Nihon Spindle Flow Forming (Spinning) machines
- Best cost performance with optimal design
- Machine specifications can be determined based on thrust measurement data obtained during the actual trials with R&D machine. Along with structural analysis, it is possible to offer “JUST-FIT” machine.
- Aggressive use of a servo motor driving method for lower running cost
- All roller units are driven by electric servo motors, which can reduce running cost by 30% to 50% against a conventional hydraulic servo method (compared to our company products). Reduction of hydraulic driving units leads to lower noise and less oil leakage.
- Independent roller control for various processes
- Each flow forming roller has their own control axis, which can be used to reduce cycle time by overlapping rollers. It is also easy to set each roller position for each axes by NC program.
- Adopt “Processing chamber” concept
-
- Processing chamber is completely isolated from the control unit and driving unit to avoid malfunction and other mechanical issues due to intrusion of coolant or sludge. This concept also offers easy cleaning of the machine.
- Optional mandrel exchange unit for smoother change-over
-
- Mandrel exchange unit and roller exchange unit are optionally available for smoother change-over due to a blocked top section of the machine.
Automotive parts
- 1Poly V pulley
A multi-groove roller is pressed against a cup-shaped blank to transfer its grooves to the blank. This is machining -free net shape process.
- 2Drive plate
It is to thicken the edge of disk blank by moving the material toward the center of the blank, which makes it possible to form 1 piece Drive Plate. Traditionally, Drive Plate consists of separate pieces with welding the disk and ring part.
- 3AT clutch
Preform is pressed against a splined mandrel by roller(s) to transfer spline profile to the preform. It is possible to secure the product strength due to its outer cylindrical shape by flow forming process. It is also possible to process hub-forming by cleaving.
- 4Brake piston
It is possible to reduce the weight and secure the strength by groove- rolling a cupshaped preform. It is to address an issue of the preform weight increase in the conventional machining method to ensure the strength of the product.
- 5Catalytic converter
and muffler
Blank tube is set in the static clamp block and rollers in the spinning head rotates and shrink the tube end diameter. Comparing to the traditional process (press + welding), spinning process can reduce the number of welding processes and production cost. It is also possible to spin eccentric and oblique process, which offers greater freedom of component design.
- 6Differential gear
It is the process to press the preform by rollers against a mandrel with inclined teeth. Traditional process requires to weld gear part and a bottom plate, whereas flow forming is able to form in single solid piece.
- 7Aluminum wheel
It is the process to press cast or forged preform against the mandrel by changing the thickness of the cylindrical portion to attain specified dimensions. It is also possible to control thickness of the product depending on the locations which need the strength or do not need the strength and eventually, it enables lighter weight and save material cost. Even casting defects (such as pin holes and shrinkage cavities) can be improved by flow forming process.
- CVT Pulley(motorcycle)
It is possible to process from the 1 piece flat disc by hub–forming, which eliminates welding as well as pre-machining and cleaving. Also it is possible to save the machining allowance due to no welding distortion.
Applications other than automotive parts
- Thermos inner bottle
Flow form the blank tube at high speed with tension to reduce the thickness less than 0.1mm.
- Gas Cylinder
Hot spinning process to shrink the rotating tube (necking process). It is possible to process in single solid piece against the conventional process in which necking portion and cylinder portion are welded. Eliminating the welding process can improve the airtightness quality.
- Printer roller
Flow form the blank tube with tension to reduce the thickness less than 0.1mm. This technology can supplement the process of long and thin products which is not able to be done by press process alone.

Features of Nihon Spindle Flow Forming (Spinning) machines
- Best cost performance with optimal design
- Machine specifications can be determined based on thrust measurement data obtained during the actual trials with R&D machine. Along with structural analysis, it is possible to offer “JUST-FIT” machine.
- Aggressive use of a servo motor driving method for lower running cost
- All roller units are driven by electric servo motors, which can reduce running cost by 30% to 50% against a conventional hydraulic servo method (compared to our company products). Reduction of hydraulic driving units leads to lower noise and less oil leakage.
- Independent roller control for various processes
- Each flow forming roller has their own control axis, which can be used to reduce cycle time by overlapping rollers. It is also easy to set each roller position for each axes by NC program.
- Adopt “Processing chamber” concept
-
- Processing chamber is completely isolated from the control unit and driving unit to avoid malfunction and other mechanical issues due to intrusion of coolant or sludge. This concept also offers easy cleaning of the machine.
- Optional mandrel exchange unit for smoother change-over
-
- Mandrel exchange unit and roller exchange unit are optionally available for smoother change-over due to a blocked top section of the machine.