产品信息
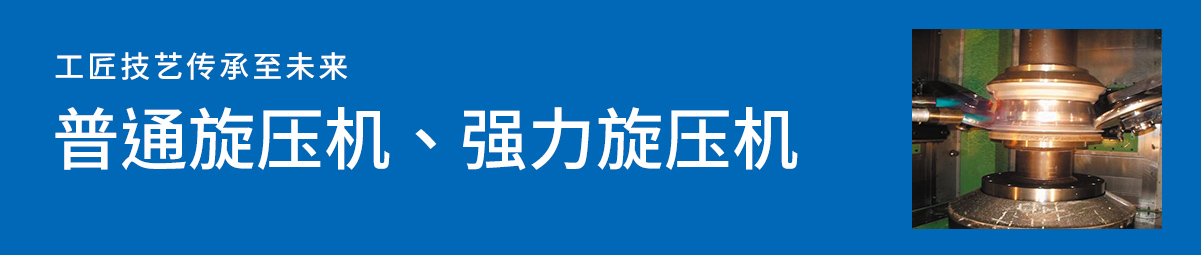

旋压加工的特点
旋压加工 是通过旋压滚轮,挤压旋转状态下的金属板材或杯状材料,进行金属的成形加工。整个加工过程 犹如捏糖人一样,可以将金属拉伸变薄,或将某一部分堆积变厚,又或将材料劈开延展...,实现传统工艺无法想像的金属成形。
旋压加工,不会产生切屑;可加工产品的形状 多样;提高了零件设计的自由度。旋压加工,可大致分为以下几种情况。

日本斯频德公司的设备特征
- 卓越设计、优良性价比
- 通过实际的加工参数,确定设备规格。通过构造解析,提供完美匹配的机器。
- 积极采用低运营成本的伺服电机驱动机构
- 滚轮单元采用电动伺服电机驱动。与以往的液压伺服式相比,运营成本可以减少30~50%(本公司内部对比)。减少液压驱动的数量、降低噪音、漏油等问题隐患。
- 各滚轮独立动作、实现多样化加工。
- 各滚轮分别配有控制轴,可以通过滚轮动作的重叠, 缩短加工时间。此外,还可以通过调整数控程序,设定、调整各滚轮的位置。
- 加工室的设计
- 加工室与控制部、驱动部完全分离,既方便清洁,又可防止冷却剂、油污等渗入设备。
- 有偿任选的模具更换装置,可以提高立式设备的作业准备效率。
- 有偿任选的模具更换装置与滚轮更换装置,解决了立式设备无法从设备上方进行换模准备的问题。
- 减薄加工
- 沿模具方向减薄材料,复制模具形状。
- 减薄加工的优势[1]
- 材料通过模具与滚轮的挤压,金属组织更加致密,可提升金属强度。加工后的材料变薄,硬化效果明显时可以省略后段的热处理工序。
- 减薄加工的优势[2]
- 通过管材端部的减径加工和胴体部分的不等厚加工,确保所需要的强度。
- 加工对象机型

日本斯频德公司的设备特征
- 最佳设计、最佳性价比
- 通过实际的加工参数,确定设备规格。通过构造解析,提供完美匹配的机器。
- 积极采用低运营成本的伺服电机驱动机构
- 滚轮单元采用电动伺服电机驱动。与以往的液压伺服式相比,运营成本可以减少30~50%(本公司内部对比)。减少液压驱动的数量、降低噪音、漏油等问题隐患。
- 各滚轮独立动作、实现多样化加工。
- 各滚轮分别配有控制轴,可以通过滚轮动作的重叠,缩短加工时间。此外,还可以通过调整数控程序,设定、调整各滚轮的位置。
- 加工室的设计
- 加工室与控制部、驱动部完全分离,既方便清洁,又可防止冷却剂、油污等渗入设备。
- 有偿任选的模具更换装置,可以提高立式设备的作业准备效率。
- 有偿任选的模具更换装置与滚轮更换装置,解决了立式设备无法从设备上方进行换模准备的问题。
- 拉深加工
- 对管材的管口进行拉深或者对胴体进行减薄加工内置零件状态下的加工
- 拉深加工的优点
- 大部分在冲压工序中需要借助多个模具来成型的复杂形状及难加工材料,在拉深加工中只需1种模具就能实现。通过在加工过程中更换工具,还能进行弯曲加工及修剪加工。

日本斯频德公司的设备特征
- 最佳设计、最佳性价比
- 通过实际的加工参数,确定设备规格。通过构造解析,提供完美匹配的机器。
- 积极采用低运营成本的伺服电机驱动机构
- 滚轮单元采用电动伺服电机驱动。与以往的液压伺服式相比,运营成本可以减少30~50%(本公司内部对比)。减少液压驱动的数量、降低噪音、漏油等问题隐患。
- 各滚轮独立动作、实现多样化加工。
- 各滚轮分别配有控制轴,可以通过滚轮动作的重叠,缩短加工时间。此外,还可以通过调整数控程序,设定、调整各滚轮的位置。
- 加工室的设计
- 加工室与控制部、驱动部完全分离,既方便清洁,又可防止冷却剂、油污等渗入设备。
- 有偿任选的模具更换装置,可以提高立式设备的作业准备效率。
-
- 有偿任选的模具更换装置与滚轮更换装置,解决了立式设备无法从设备上方进行换模准备的问题。
- 劈开加工
- 将材料劈开后,进行Y字型或T字型成形加工一体化、无焊接成形
- 劈开加工的优势
- 通常,花键成形使用切削工艺、凸台成形使用焊接工艺。如果使用旋压工艺,则无需切削、或焊接就可以完成产品的成形加工。
- 加工对象机型

日本斯频德公司的设备特征
- 最佳设计、最佳性价比
- 通过实际的加工参数,确定设备规格。通过构造解析,提供完美匹配的机器。
- 积极采用低运营成本的伺服电机驱动机构
- 滚轮单元采用电动伺服电机驱动。与以往的液压伺服式相比,运营成本可以减少30~50%(本公司内部对比)。减少液压驱动的数量、降低噪音、漏油等问题隐患。
- 各滚轮独立动作、实现多样化加工。
- 各滚轮分别配有控制轴,可以通过滚轮动作的重叠,缩短加工时间。此外,还可以通过调整数控程序,设定、调整各滚轮的位置。
- 加工室的设计
- 加工室与控制部、驱动部完全分离,既方便清洁,又可防止冷却剂、油污等渗入设备。
- 有偿任选的模具更换装置,可以提高立式设备的作业准备效率。
- 有偿任选的模具更换装置与滚轮更换装置,解决了立式设备无法从设备上方进行换模准备的问题。
- 增厚加工
- 聚集材料,进行局部增厚
- 增厚加工的优势
- 实现驱动盘的盘面、内齿的无焊接、一体化。此外,可以通过滚轧成形,将滚轮的形状复制到产品上,实现环形凹槽或齿轮的滚轧成形。
- 加工对象机型

日本斯频德公司的设备特征
- 最佳设计、最佳性价比
- 通过实际的加工参数,确定设备规格。通过构造解析,提供完美匹配的机器。
- 积极采用低运营成本的伺服电机驱动机构
- 滚轮单元采用电动伺服电机驱动。与以往的液压伺服式相比,运营成本可以减少30~50%(本公司内部对比)。减少液压驱动的数量、降低噪音、漏油等问题隐患。
- 各滚轮独立动作、实现多样化加工。
- 各滚轮分别配有控制轴,可以通过滚轮动作的重叠,缩短加工时间。此外,还可以通过调整数控程序,设定、调整各滚轮的位置。
- 加工室的设计
- 加工室与控制部、驱动部完全分离,既方便清洁,又可防止冷却剂、油污等渗入设备。
- 有偿任选的模具更换装置,可以提高立式设备的作业准备效率。
- 有偿任选的模具更换装置与滚轮更换装置,解决了立式设备无法从设备上方进行换模准备的问题。
- 滚轧成形加工
- 将滚轮形状复制到材料上,进行环形凹槽或齿形的成形加工。
- 滚轧成形加工的优势
- 实现驱动盘的盘面、内齿的无焊接、一体化。此外,可以通过滚轧成形,将滚轮的形状复制到产品上,实现环形凹槽或齿轮的滚轧成形。
- 加工对象机型

日本斯频德公司的设备特征
- 最佳设计、最佳性价比
- 通过实际的加工参数,确定设备规格。通过构造解析,提供完美匹配的机器。
- 积极采用低运营成本的伺服电机驱动机构
- 滚轮单元采用电动伺服电机驱动。与以往的液压伺服式相比,运营成本可以减少30~50%(本公司内部对比)。减少液压驱动的数量、降低噪音、漏油等问题隐患。
- 各滚轮独立动作、实现多样化加工。
- 各滚轮分别配有控制轴,可以通过滚轮动作的重叠,缩短加工时间。此外,还可以通过调整数控程序,设定、调整各滚轮的位置。
- 加工室的设计
- 加工室与控制部、驱动部完全分离,既方便清洁,又可防止冷却剂、油污等渗入设备。
- 有偿任选的模具更换装置,可以提高立式设备的作业准备效率。
- 有偿任选的模具更换装置与滚轮更换装置,解决了立式设备无法从设备上方进行换模准备的问题。
汽车相关零部件
- 1V 型皮带轮
在杯状材料上旋压凹槽,可以确保凹槽底部的板厚,实现轻量化的同时保持零件的强度。
- 2驱动盘
将板材外缘的材料堆往中央,实现外缘的环形成型。
- 3AT 离合器鼓
旋压材料至齿形模具,复制齿模形状的加工方法。产品外周相连,可以制约高转速下的产品变形。还可以通过劈开加工,进行凸台部位的一体成形。
- 4刹车活塞
在杯状材料上旋压凹槽,可以确保凹槽底部的板厚,实现轻量化的同时保持零件的强度。
- 5触煤转换器・消音器
固定管坯,外圈用公转的滚轮进行缩管加工。与以往的(冲压 + 焊接)工序相比,可以大幅度减少焊接工序并减少生产成本。 相对于管坯中心线,可以平行移动或者倾斜缩管部分中心线,增加零件设计的自由度。
- 6变速器齿轮
在带有斜齿的模具上,用滚轮按压材料进行加工。
- 7铝圈
铸造或锻造材料,通过旋压改变轮辋部位的厚度,加工至规定尺寸。需要强度的部位保持厚壁,不需要强度的部位加工减薄,实现产品的轻量化、削减材料成本。还可以改善铸造缺陷(气泡、缩孔)。
- CVT 皮带轮(摩托车)
将板材的材料向凸台部位堆积,实现一体成型,可以省略焊接加工以及前端的切削、清洗工序。由于没有焊接变形,可以减少切削量。
汽车零部件之外的加工案例
- 保温杯
拉伸管坯的同时,进行高速旋压,加工后板厚小于0.1mm。
- 高压气瓶
旋转管坯的同时,进行热旋缩颈加工。以往缩颈部分和圆筒部分是分别成型后焊接而成,如今可以实现一体成型。既可以取消焊接工序,又可以提升气密性的质量。
- 打印机滚轮
拉伸管坯的同时,进行减薄旋压,加工后板厚小于0.1mm。可以弥补冲压工艺难以实现的超长、薄壁产品的加工。

日本斯频德公司的设备特征
- 最佳设计、最佳性价比
- 通过实际的加工参数,确定设备规格。通过构造解析,提供完美匹配的机器。
- 积极采用低运营成本的伺服电机驱动机构
- 滚轮单元采用电动伺服电机驱动。与以往的液压伺服式相比,运营成本可以减少30~50%(本公司内部对比)。减少液压驱动的数量、降低噪音、漏油等问题隐患。
- 各滚轮独立动作、实现多样化加工。
- 各滚轮分别配有控制轴,可以通过滚轮动作的重叠,缩短加工时间。此外,还可以通过调整数控程序,设定、调整各滚轮的位置。
- 加工室的设计
-
- 加工室与控制部、驱动部完全分离,既方便清洁,又可防止冷却剂、油污等渗入设备。
- 有偿任选的模具更换装置,可以提高立式设备的作业准备效率。
-
- 有偿任选的模具更换装置与滚轮更换装置,解决了立式设备无法从设备上方进行换模准备的问题。