Mixers
WONDER KNEADER (G III Technology)
Possibility of Single-Stage Mixing by Wonder Mixer (G III Technology)
1.Introduction
Mixing of rubbers generates heat according to formulations. This tendency is more apparent with the Mixers of a larger capacity, and two-stage (A, B) mixing is often used to protect the rubber stock from scorching due to the rise of the mixing temperature. This situation has led to the study on a single-stage mixing (including mixing of curing accelerator) using a Mixer of a high cooling efficiency that will prevent the temperature from rising to a scorching level of the rubber compounds.
A simple model analysis of how the rubber inside the Mixer lost its temperature to the cooling water revealed that cooling was limited to the surface of the rubber in direct contact with the chamber or the rotor, and that the rubber under the surface remained uncooled. An intermesh type Mixer was once proposed to improve the cooling effect, but a tangential type Mixer was finally chosen because of its material bitability and the ease of discharge and cleaning that determined efficiency of small-lot, wide-variety production for which the rubber Mixer process was normally used. A target temperature of 120 or lower was chosen for the single-stage mixing.
2.Experiments
- Rubber material
Mixing was tested using NBR, ACM and CR having different Mooney levels. - Relationship between rubber thickness in the Mixer and mixing temperature
The mixing temperature increases with the increase in the Mixer capacity. A detailed study with regard to the rubber thickness in the Mixer revealed a linear relationship between the mixing temperature and the rubber thickness. With this finding, the rubber thickness was calculated that corresponded to the mixing temperature of around 120, and the rotor was designed that would produce that thickness.
3.Results and Considerations
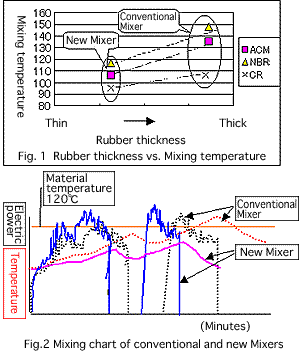
- Mixing temperature
Materials of varying viscosities (NBR, CR and, ACM; 55 liters each) were tested in the conventional and the new Mixers. Temperature readings from this comparative experiment are shown in Figures 1 and 2. - Material properties
The conventional Mixer uses Open roll as final mixing (two-stage mixing) and the new Mixer complete with final mixing (single-stage mixing). The comparative test revealed the new Mixer surpasses in performance. - Possibility of single-stage mixing by Wonder Mixer (G III Technology)
- The new Mixer allows mixing at low temperatures and suggests that it is capable of single-stage mixing of materials of varying viscosities.